In the world of metal fabrication, aluminum laser cutting has emerged as an innovative, efficient, and high-quality option for numerous industries. This advanced method offers a multitude of benefits over traditional cutting methods, allowing for greater precision, speed, and flexibility in design. In this article, we will explore aluminum laser cutting and its advantages, compare it to alternative cutting methods, and provide guidance on selecting the right laser cutting service for your project.
Table of Contents
An Overview of Aluminum Laser Cutting
What is Aluminum Laser Cutting?
Aluminum laser cutting is a highly precise and efficient method of metal fabrication. It involves using a focused, high-intensity laser beam to remove material from an aluminum sheet or workpiece. The laser beam is so powerful that it can rapidly heat, melt, and vaporize the aluminum, creating a clean and precise cut. This technology has revolutionized the manufacturing industry, allowing for complex and intricate designs to be cut with ease.
Aluminum laser cutting is a non-contact process, which means that the laser beam does not physically touch the material. This eliminates the risk of contamination and damage to the workpiece, resulting in a high-quality finished product. Additionally, the process is highly automated, which reduces the need for manual labor and increases efficiency.
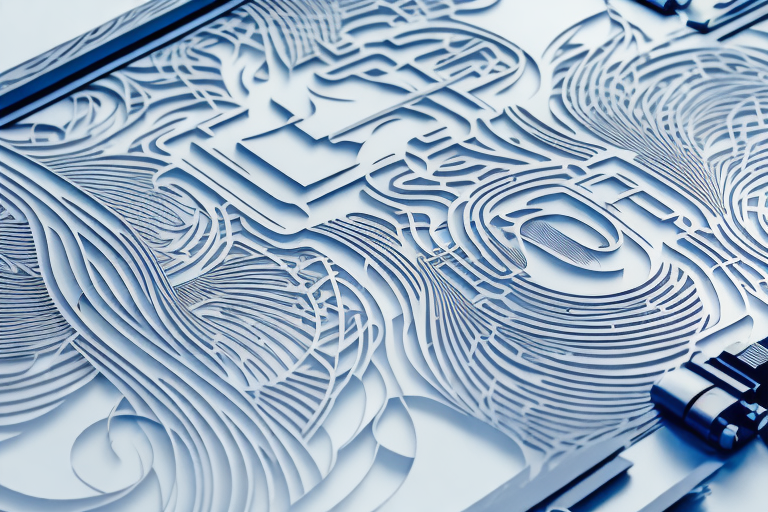
The Laser Cutting Process
The process of aluminum laser cutting is straightforward and efficient. It begins with a digital vector file that contains the design or pattern to be cut. This file is then sent to a computer numerical control (CNC) machine, which guides the laser beam’s movement across the aluminum workpiece.
As the laser beam traverses the material, it rapidly heats and melts the aluminum, creating a narrow kerf width and a smooth edge finish. The CNC machine controls the speed and intensity of the laser beam, ensuring that the cut is precise and accurate.
Once the desired pattern is achieved, the aluminum workpiece can either be removed from the machine or further processed for additional operations. This versatility makes aluminum laser cutting a popular choice for a wide range of industries, including aerospace, automotive, and electronics.
The Benefits of Aluminum Laser Cutting
Aluminum laser cutting offers numerous benefits over traditional metal fabrication methods. One of the primary advantages is the precision and accuracy of the cut. The laser beam can cut through aluminum with incredible speed and accuracy, resulting in a high-quality finished product.
Another benefit is the flexibility of the process. Aluminum laser cutting can be used to cut a wide range of shapes and designs, from simple to complex. This versatility makes it an ideal choice for industries that require intricate geometries.
Finally, aluminum laser cutting is a cost-effective and efficient method of metal fabrication. The process is highly automated, which reduces the need for manual labor and increases productivity. This, in turn, reduces costs and lead times, making it an attractive option for businesses looking to streamline their manufacturing processes.
Conclusion
Aluminum laser cutting is a highly precise and efficient method of metal fabrication. It offers numerous benefits over traditional metal cutting methods, including precision, flexibility, and cost-effectiveness. Whether you are in the aerospace, automotive, or electronics industry, aluminum laser cutting can help you achieve your manufacturing goals with ease.
Advantages of Aluminum Laser Cutting
Precision and Accuracy
One of the greatest advantages of aluminum laser cutting is its ability to provide unmatched precision and accuracy in comparison to traditional cutting methods. The high-energy laser allows for intricate and complex geometries to be cut with ease, resulting in parts that meet exacting specifications. In addition, the non-contact nature of the process minimizes material deformation and eliminates the need for additional finishing operations, further enhancing the accuracy of the final product.
Speed and Efficiency
Another significant advantage of aluminum laser cutting is its speed and efficiency. Laser cutting machines can process large volumes of material in a relatively short period, resulting in quicker turnaround times and increased productivity. This reduction in processing time also translates to lower overall costs, making it a cost-effective choice for many industries.
Material Conservation and Waste Reduction
Aluminum laser cutting not only provides superior precision and speed but also contributes to material conservation and waste reduction. The focused laser beam allows for minimal kerf width and removal of material, reducing the amount of material wasted during the cutting process. Furthermore, the non-contact nature of the process reduces material deformation and the need for additional finishing operations, further minimizing waste and reducing overall production costs.
Flexibility in Design
One of the most appealing aspects of aluminum laser cutting is the flexibility it offers in terms of design. Its ability to cut intricate and complex geometries makes it an excellent option for industries requiring precise components with unique shapes and patterns. This flexibility enables designers to push the boundaries of creativity and innovation, resulting in higher-quality and more imaginative products.
Comparing Aluminum Laser Cutting to Traditional Methods
Aluminum Laser Cutting vs. Plasma Cutting
Compared to plasma cutting, aluminum laser cutting offers greater precision and accuracy, as well as reduced kerf width and material waste. Additionally, the non-contact nature of laser cutting results in less heat-affected zones and material deformation, reducing the need for further finishing operations. Whilst plasma cutting can be faster and better suited for thicker materials up to 160mm, aluminum laser cutting is the superior choice for intricate designs and thinner materials.
Aluminum Laser Cutting vs. Waterjet Cutting
Waterjet cutting is another alternative cutting method that uses a high-pressure jet of water mixed with abrasive materials to cut through material. Although its cutting force is far less than lasers, and it can cut thicker materials, it lacks the precision and accuracy of aluminum laser cutting. Furthermore, the waterjet process can result in a rougher finish on the cut edge, often requiring further finishing operations. In terms of speed, efficiency, and material waste reduction, aluminum laser cutting is the superior choice for most applications.
Aluminum Laser Cutting vs. Mechanical Cutting
Mechanical cutting methods, such as shearing or milling, involve physical contact between the cutting tool and the material. While these methods can be cost-effective for simple cuts and high-volume production, they lack the precision, accuracy, and flexibility offered by aluminum laser cutting. Additionally, mechanical cutting processes can introduce stress and potential deformation to the material, especially in intricate or close-tolerance designs. For precise, intricate, and complex geometries, aluminum laser cutting is the clear winner.
Applications of Aluminum Laser Cutting
Aerospace and Automotive Industries
Aluminum laser cutting is heavily utilized in the aerospace and automotive industries due to its high level of precision, accuracy, and flexibility in design. Components such as lightweight, intricate brackets, heat sinks or control panels can be fabricated efficiently and cost-effectively using this method.
Electronics and Telecommunications
The electronics and telecommunications industries also benefit from aluminum laser cutting, as it allows for the precise manufacturing of intricate components, such as housings, covers, and heat sinks required for devices like smartphones, laptops, and other electronic equipment.
Construction and Infrastructure
In construction and infrastructure projects, aluminum laser cutting can be used to create intricate architectural elements, custom brackets, and decorative panels. Its ability to cut fine and detailed patterns makes it a popular choice in these industries.
Art and Design
Artists and designers also utilize aluminum laser cutting for the creation of intricate sculptures, installations, and decorative pieces. The flexibility and precision offered by this cutting method encourage creativity and innovative design solutions.
Choosing the Right Laser Cutting Service
Factors to Consider
When selecting a laser cutting service provider, several factors should be considered, including reputation, experience, equipment, and customer support. Look for providers that have a proven track record of delivering high-quality work and have invested in advanced machinery to ensure optimal results.
Evaluating Quality and Expertise
Assess the quality and expertise of a laser cutting service provider by examining their portfolio and customer testimonials. Look for companies that have experience working with industries similar to yours and have successfully completed projects with comparable levels of complexity.
Cost and Turnaround Time
While cost is an important factor, it should not be the sole determinant in your decision-making process. Instead, consider the overall value, including quality, customer support, and turnaround time provided by the laser cutting service. The best providers will work closely with their clients to ensure a smooth, efficient, and cost-effective experience.